Void / Chair
01.15 – 04.15
“Void/Chair” was an exercise in manufacturing a chair that was both lightweight and durable. The chair’s rudimentary dimensions were based off of the 4×4 foot constraints of the CNC Bed we were using. Each chair would eventually be cut out of a 2×4 foot section of a CNC Bed, allowing us to cut two chairs at any given time. Using structural analysis on multiple iterations of our design, we determined where it was appropriate to remove material in order to create a relationship between weight and durability.
Results
The results gave the chair enough strength to withstand a large person while removing 62% of the excess material and weight. Aside from the milled piece of plywood, the chair is composed of a single steel joint, epoxy, varnish and coat of orange paint.
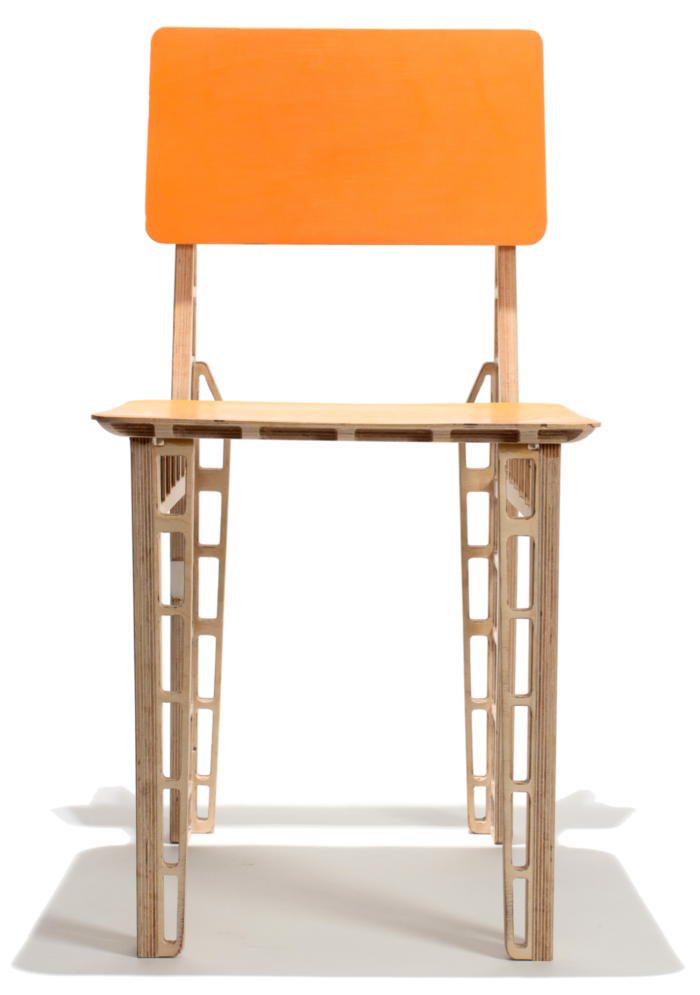

Critical connection between front legs and seat

View of back

Location of steel rod, cast with epoxy
Design Process
01: Mapping to CNC Bed
Using a preliminary Grasshopper script, all components of the chair were mapped from a live model onto a 2D plane. Here, the pieces were arranged within the confined 2×4 foot dimensions set within the CNC Bed. By looking at both a live model and a planar view of what would be cut on the CNC, we were able to make informed decisions about the sizes of individual pieces.

02: Loading Simulation
(a) Simulation: The first iteration of testing used the physics engine Kangaroo and relied on looking at how forces distributed through a triangular grid. The results helped give a visual understanding of the forces, but proved to be overly complicated.
(b) Design: To reach a ‘minimum’ material usage iterative solving techniques were used. Essentially, the loading was simulated on the chair and then was ‘redrawn’ through the script. This can be done thousands of times with the help of a computer.
(c) Tuning: Where the seat met the back legs, there was previously lots of stress. The area surrounding this crucial point was reinforced.

(b)

(c)
03: Prototype
After finalizing the script, a 1-to-1 model was built in order to ensure things fit together properly.

Critical connection between front legs and seat

View of back

Location of steel rod, cast with epoxy
04: Final Script
Our iterative model needed to know what the structure looked like when loaded. The Kangaroo physics engine was used in the final script for simulating compressive and tensile forces. The script was responsible for rebuilding surfaces in Rhinoceros using the data found in the Kangaroo physics engine.

05: Final Design
The results gave the chair enough strength to withstand a large person while reducing 62% of the excess material and weight. Since, the voided space was milled-out and never used, in real-world application this design would be made out of Polypropylene to maximize use of material while still creating a strong and durable chair.

Before Voids
Total Weight:
11.30 kg / 24.90 lbs
Area:
.0188 M(^3)

After Voids
Total Weight:
4.37 kg / 9.6lbs
Area:
.0073 M(^3)
Orthographic
Drawings




Front Elevation
Side Elevation
Back Elevation
Plan
